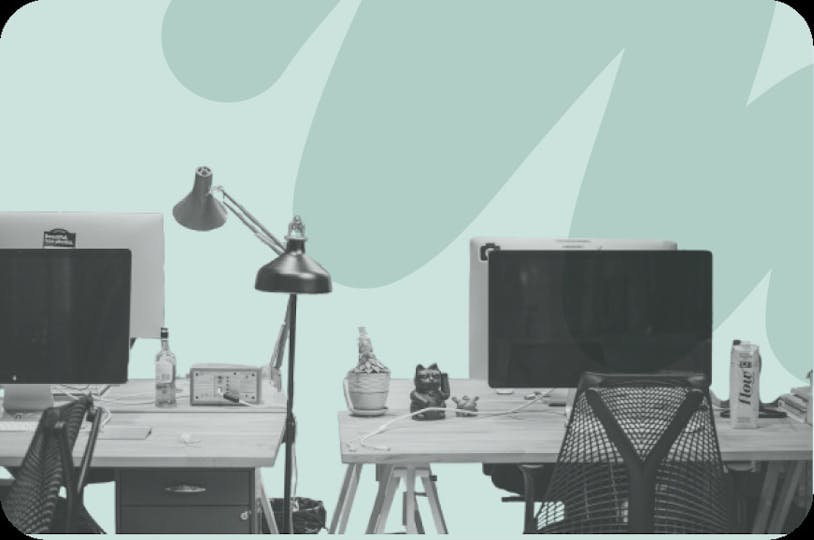
10 Reasons to Track a Corporate Carbon Footprint
In this article, we’ll explain what a corporate carbon footprint is, why it’s important, how it is measured, and reasons why your company should track it too.
ESG / CSR
Industries
When starting a business in the midst of climate change, it can be confusing to determine which approach to management is the best way to ensure ultimate efficiency and waste reduction to adhere with various standards, stakeholder expectations, and ensure customer satisfaction – and luckily, lean management could be the answer.
Initially developed by Toyota, lean management offers a way for business to improve upon business efficiency – which can lead to long-term success.
In this article, we’ll explain what lean management is, the five principles, and how your company can get started with lean management.
Lean management is a systematic approach to boosting efficiency and avoiding waste in business practices.
The ideals of lean management originated from Toyota’s Production System (TPS) in the 1940s, and now serves as an applicable method across various industries to help encourage business efficiency and waste reduction.
Overall, a lean management system allows companies to reevaluate their current business model and determine which practices are currently serving them towards business growth – or which processes are creating inefficiencies and need to be improved or eliminated to maximise productivity and long-term success.
Lean management is important as it helps businesses to enhance their overall productivity and potentially elicit long-term lucrative success moving forward.
This is because lean management helps companies to zone in on improvement such as by looking to cut back on business operations, streamline processes, and deliver higher quality products and services.
Here are some of the reasons why lean management is important:
Lean management works when companies adhere to the following set of principles:
The table below will compare and contrast these lean management methods and tools to help you decide which one is best for your business:
Method/Tool | Description | Best For | Key Benefits | Potential Limitations |
---|---|---|---|---|
5S Methodology | A workplace organisation system focusing on Sort, Set in order, Shine, Standardise, and Sustain. | Manufacturing, offices, warehouses, healthcare | - Improves workplace efficiency - Reduces waste - Enhances safety and organisation |
- Requires ongoing discipline - Can be time-consuming to implement initially |
Kanban System | A visual workflow tracking system that manages work-in-progress and optimises flow. | Software development, project management, production lines | - Reduces bottlenecks - Improves task visibility - Enhances team collaboration |
- Requires continuous updates - Can become ineffective if overloaded |
Value Stream Mapping (VSM) | A process analysis tool that maps current and future workflows to identify inefficiencies. | Manufacturing, logistics, service industries | - Identifies areas for process improvement - Reduces lead times - Enhances overall efficiency |
- Can be complex and time-consuming - Requires detailed data collection |
PDCA Cycle | A four-step continuous improvement model: Plan, Do, Check, Act. | Any industry seeking ongoing improvements | - Encourages problem-solving - Ensures continuous improvement - Works in all business areas |
- Can be slow to show results - Needs commitment for sustained impact |
There are five main principles of lean management: which is to identify customer values, map the value chain, create a continuous flow, establish a pull-based system, and to pursue continuous improvement.
Here’s a breakdown of the five main principles of lean management:
As we’ve already established, this first principle of lean management focuses on the product and service the business provides to its customers – and how it can adjust the product or service it offers to better fit the needs of their consumers.
This helps businesses to determine where their workflow and business processes can be improved.
This is when companies will then adjust the workflow of their business to improve upon product or service value.
As a result, this will include reviewing all of the areas of the development of a product or service – from the various suppliers, stakeholders, and transportation services used to deliver the end product to the customer.
In lean management, companies will determine which steps and processes can be deemed as no longer necessary.
Once your company’s value chain has been assessed, it will then be necessary to adjust each team’s workflow – which can be done by breaking down larger tasks into smaller ones to aid in the transition to improved workflow.
Ensuring that an effective pull system is intact can help your business to guarantee it continues to value its customers and map its value stream accordingly.
As a whole, employing a pull system will help companies to provide the customer-focused products and services they are striving to – as depicted in the first principle of lean management.
One the first four principles have been implemented, your company is now operating under a lean management system – but the fifth and perhaps most crucial element of a lean management system is striving for continuous improvement.
This includes holding periodic meetings with your staff to ensure all of the essential components to ensure lean management remains intact, or even something simpler such as offering a “suggestion box” for employees to share new ways to keep optimising business practices.
Overall, the principles of lean management help a company to improve upon its current business model and ensure continuous consistency and customer satisfaction – all of which can help a business to achieve long-term growth and sustainability.
There are several benefits of lean management, such as greater efficiency, cost reduction, improved team management, and better quality products.
Lean management allows for faster workflows, fewer delays, reduced operational costs, and dedication to improving products and processes for increased customer satisfaction and employee productivity.
Here are some of the additional benefits of lean management:
Ultimately, the principles of lean management will allow for a long-term sustainable production process and will also benefit your employees and customers.
It may be intimidating to employ a method as seemingly complex as lean management, but the truth is – lean management can be incorporated into via small, but effective steps.
Remember, implementing lean management with manageable steps helps to ensure that all of your employees will be committed to long-term, continuous improvement.
Overall, by following these steps – your businesses can create a more efficient, cost-effective, and adaptable work environment, where its management will fall under the umbrella of lean management.
It may seem overwhelming, but remember – starting small and engaging your team members are integral to success, and you’ll always have third-party companies like Greenly here to help you implement tactics like lean management and other sustainable initiatives along the way.
If reading this article about lean management has inspired you to consider your company’s own carbon footprint, Greenly can help.
At Greenly we can help you to assess your company’s carbon footprint, and then give you the tools you need to cut down on emissions. We offer a free demo for you to better understand our platform and all that it has to offer – including assistance on how to reduce emissions, optimise energy efficiency, and more to help you get started on your climate journey.
Learn more about Greenly’s carbon management platform here.
Business Map https://businessmap.io/lean-management/what-is-lean-management
LinkedIn https://www.linkedin.com/pulse/five-principles-lean-management-ryan-e-b-heri-pmp/
Manutan https://www.manutan.com/blog/en/glossary/lean-management-definition-and-tools
EPA https://www.epa.gov/sustainability/lean-thinking-and-methods-kaizen
Indeed https://www.indeed.com/career-advice/career-development/pull-system
The Lean Wayhttps://theleanway.net/The-8-Wastes-of-Lean