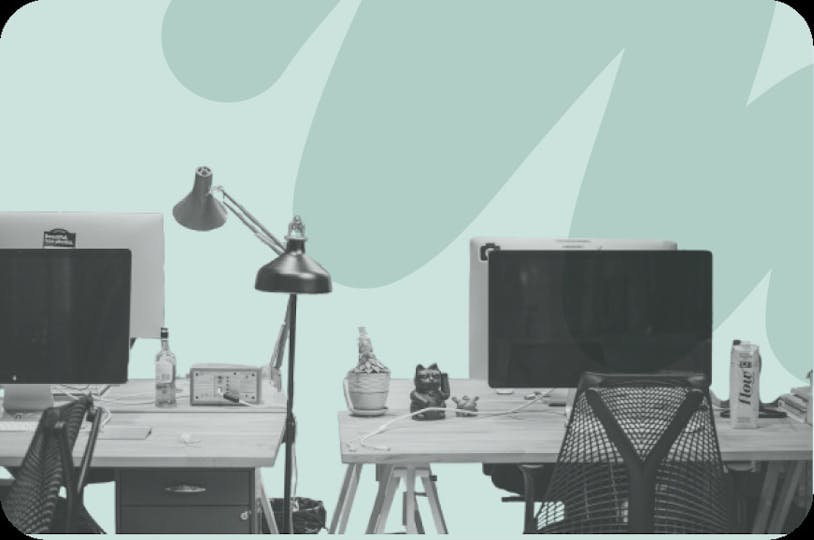
10 Reasons to Track a Corporate Carbon Footprint
In this article, we’ll explain what a corporate carbon footprint is, why it’s important, how it is measured, and reasons why your company should track it too.
ESG / CSR
Industries
From the clothes we wear to the phones in our pockets, most of the goods we rely on have travelled thousands of miles before reaching us. Behind each item lies a network of suppliers, manufacturers, freight companies, distributors, and retailers – all working across borders to keep shelves stocked and businesses running.
These global supply chains are the backbone of modern commerce. They’ve enabled companies to optimise costs, access international talent and resources, and expand into new markets. But as recent years have shown, they are also vulnerable to everything from pandemics and political tensions to climate change and raw material shortages.
Supply chains are now central to conversations about national security, climate strategy, corporate sustainability, and economic resilience. Across industries, regulatory complexity and growing ESG expectations are forcing a rethink of global sourcing and operational models.
In this article, we’ll explore how global supply chains work, the key challenges they’re facing, and what the future might look like – including a closer look at the environmental and climate-related pressures reshaping supply chains today.
This process rarely happens in a straight line. Instead, products often zigzag across the globe. Parts might be made in one country, assembled in another, then sold in multiple markets. It’s not unusual for a single item to pass through multiple countries before it ends up with a customer.
To keep everything running smoothly, companies rely on a web of suppliers, freight carriers, customs brokers, distributors, retailers, and increasingly, digital platforms to track and manage the process. Timelines are tight, margins are often narrow, and the expectation is that goods arrive on time and at low cost, no matter how complex the journey.
For years, the focus has been on maximising efficiency. Just-in-time inventory systems, lean manufacturing, and global outsourcing have helped companies reduce costs and streamline operations. But this efficiency often comes at the expense of flexibility, and that trade-off has become more evident in the face of recent disruptions.
Today’s supply chains are more interconnected than ever before, but they’re also more exposed. A delay in one part of the chain - whether it’s a factory shutdown, port congestion, or a missing shipment - can have knock-on effects that ripple across multiple industries and regions.
Global supply chains rely on a whole network of actors to function, and they all play a role in getting goods from one side of the world to the other:
Almost every sector is touched by global supply chains, from automotive and electronics to fashion, food, pharmaceuticals, and even renewable energy. A laptop might rely on semiconductors from Taiwan, rare earth metals from Africa, and assembly plants in China. A cotton T-shirt could involve cotton grown in India, woven in Bangladesh, dyed in Turkey, and sold in Europe or North America.
Over the last few decades, global supply chains have been key to driving growth and reducing costs. By sourcing materials or production where it’s most efficient, businesses have been able to scale quickly and keep prices competitive. But this interconnectedness also means that when something goes wrong in one part of the world, the ripple effects can be felt everywhere else.
We’ve seen this play out in recent years. Shortages of semiconductors have held up car production. Port delays have left supermarket shelves empty. Extreme weather events have disrupted crop yields and cut off transport routes. Each example highlights just how dependent modern economies are on supply chains working as intended, and just how fragile those systems can be.
Global supply chains have always faced a degree of uncertainty; fluctuating demand, supplier delays, or bad weather are nothing new. But in recent years, the risks have intensified.
From geopolitical tensions and labour shortages to pandemics, extreme weather, and mounting regulatory demands, global supply chains are now under pressure. And because these challenges are often interconnected, even a small disruption can quickly escalate, exposing weaknesses, increasing costs, and leaving businesses scrambling to adapt.
Some of these risks are short-term and highly visible (a factory shutdown, a strike, a shipping delay). Others are slower moving but no less serious (the long-term decline in key natural resources, or the shifting expectations around environmental and social responsibility in the supply chain.
Risk category | What it involves |
---|---|
Geopolitical and economic instability | Trade disputes, sanctions, armed conflicts, and rising protectionism can delay shipments, raise costs, or restrict access to key materials. |
Labour and skills shortages | Recruitment challenges, skills gaps, and workforce shortages in logistics, manufacturing, and warehousing cause delays, reduce flexibility, and increase costs. |
Public health disruptions | Pandemics or regional outbreaks can shut down factories, close borders, and create sudden demand shifts, exposing fragile supply chains. |
Material scarcity and resource risk | Rising global demand, concentrated production regions, and environmental stress are making raw materials like lithium, copper, and semiconductors harder to secure. |
Regulatory complexity and fragmentation | Varying international rules on trade, sustainability, and due diligence increase compliance burdens and create reputational and operational risk. |
Environmental and climate-related risks | Scope 3 emissions, resource depletion, and climate impacts like floods, droughts or wildfires can disrupt supply routes and undermine long-term stability. |
Political tensions and economic uncertainty are increasingly disrupting global supply chains.
Trade disputes, sanctions, and shifting alliances can raise costs, delay shipments, or force companies to rethink sourcing strategies. The US–China trade war, for example, prompted many firms to diversify away from Chinese manufacturing, creating new complexities in the process.
Armed conflicts are another major disruptor. The war in Ukraine has affected global flows of energy, grain, and metals, fuelling shortages and pushing up prices across multiple sectors. Sanctions and export controls have further strained access to key materials.
More recently, Houthi attacks on commercial vessels in the Red Sea have forced major shipping lines to reroute around the southern tip of Africa, significantly increasing journey times and transport costs. For companies reliant on fast, reliable shipping between Asia and Europe, these diversions have added weeks to delivery schedules and put pressure on already stretched logistics networks.
Even in the absence of conflict, rising protectionism and efforts to prioritise domestic production are making it harder to operate across borders. As a result, supply chain decisions increasingly have to account for political risk, not just cost and efficiency.
A shortage of workers is another issue weighing heavily on global supply chains. Many sectors are struggling to recruit and retain staff. The pandemic accelerated early retirements and career changes, while stricter immigration rules in some countries have reduced the pool of available workers. Meanwhile, demand for logistics and e-commerce roles has soared, outpacing supply in many regions.
In some cases, the issue is less about numbers and more about skills. As supply chains become more digital and automated, businesses need workers who can manage data systems, robotics, or AI-driven platforms – roles that are often hard to fill.
When labour is in short supply, the knock-on effects can be significant. Delays, backlogs, rising costs, and reduced flexibility all impact the flow of goods. In some cases, manufacturers are being forced to scale back production or reroute shipments simply because the people needed to keep things moving aren’t there.
Solving the problem isn’t easy. It means investing in training, improving working conditions, and in some cases, redesigning operations to be less labour-intensive. But in the short term, labour shortages remain a major constraint, particularly in logistics, warehousing, and manufacturing
The COVID-19 pandemic exposed just how fragile global supply chains can be in the face of a major health crisis. Factory closures, border restrictions, and sudden shifts in consumer demand caused widespread delays and shortages. Essential items became hard to source, while shipping backlogs and port closures created bottlenecks that rippled across industries.
Although the disruptions are a thing of the past, the experience has left a lasting impact. Many companies are now rethinking their dependence on single suppliers or regions, and are building in greater flexibility through dual sourcing, local production, or buffer inventory.
It’s possible that other health-related disruptions (future pandemics and regional disease outbreaks) could cause similar shocks. As a result, resilience planning now increasingly includes public health risk, not just logistical or geopolitical factors.
Supply chains depend on a steady flow of raw materials, but access to those materials is becoming more uncertain. From semiconductors and rare earth elements to lithium, copper, and even basic agricultural inputs, global demand is rising fast. At the same time, production is often concentrated in just a few countries, making supply chains vulnerable to political shifts, natural disasters, or export restrictions.
We’ve already seen the impact. The global chip shortage brought entire industries to a standstill, while limited access to key metals has raised concerns about the pace of the energy transition. In agriculture, droughts and extreme weather are disrupting crop yields, creating knock-on effects for food and textile supply chains.
Longer term, resource depletion is another growing concern. Some materials are finite. Others are becoming harder to extract without significant environmental or social costs. As a result, companies are increasingly looking to diversify sources, invest in recycling, or reduce reliance on high-risk materials altogether.
Global supply chains often stretch across multiple jurisdictions, which makes staying compliant a challenge. Trade regulations, customs procedures, product standards, and environmental rules vary widely between countries and are constantly evolving.
A material that can be imported freely into one region might be restricted or heavily taxed in another. Packaging or labelling requirements can differ not just by country, but sometimes by state or province.
In recent years, a wave of new regulations focused on sustainability and human rights has added another layer of complexity. Many companies are now required to trace the origins of their materials, assess environmental and social risks in their supply chains, and report on their impacts in line with ESG frameworks or due diligence laws.
This fragmentation creates both an administrative burden and reputational risk. Failing to comply – even unknowingly – can result in fines, shipment delays, or public backlash. But trying to track and manage every requirement across a global supplier network is no small task.
For businesses operating internationally, keeping up with this shifting regulatory landscape has become complex and often requires collaboration across legal, compliance, procurement, and sustainability teams.
For many businesses, the majority of their environmental impact lies outside their own operations, in the materials they source, the way products are manufactured, and how goods are transported. As expectations around sustainability rise, companies are under growing pressure to understand and reduce the environmental footprint of their supply chains.
One of the biggest concerns is emissions. Transport, raw material extraction, and outsourced production are all major contributors to a company’s Scope 3 emissions – the indirect emissions that occur across the value chain. In fact, for most organisations, these emissions far exceed those from direct operations.
But emissions aren’t the only issue. Supply chains also drive resource depletion, waste generation, pollution, and land-use change. Sectors like food, fashion, and electronics are particularly resource-intensive, with global supply chains that rely heavily on water, energy, and non-renewable materials.
At the same time, climate change itself is putting supply chains at risk. More frequent floods, droughts, storms, and wildfires are damaging infrastructure, disrupting transport routes, and affecting the availability of raw materials.
A clear example is the ongoing drought that is impacting the Panama Canal. With water levels at historic lows, authorities were forced to restrict the number of daily vessel transits and impose weight limits, slowing down one of the world’s busiest shipping routes. Some vessels have had to be rerouted thousands of miles around South America, increasing delivery times, costs, and emissions, and highlighting just how exposed global logistics are to the effects of extreme weather.
This makes climate adaptation just as important as emissions reduction. Businesses need to understand where their supply chains are most vulnerable and take steps to build resilience, whether that means diversifying suppliers, reinforcing infrastructure, or shifting to lower-risk regions.
Technology is playing a key role. Advances in digital tools like AI-powered forecasting, real-time tracking, and blockchain-enabled traceability are helping businesses gain better visibility, anticipate disruptions, and reduce waste.
These tools are also making it easier to monitor emissions and environmental impact across the value chain, something that’s becoming essential as regulations tighten and stakeholders demand greater accountability.
At the same time, many businesses are rethinking geography. The drive to reshore or nearshore production, whether to reduce risk, meet local content requirements, or shorten lead times, is reshaping global trade patterns. While cost remains a factor, it’s no longer the only consideration.
There’s also growing momentum behind circular economy principles; designing products to last longer, be reused, or made from recycled materials. For supply chains, this means building in new capabilities: take-back systems, reverse logistics, and partnerships with recyclers or remanufacturers.
Above all, supply chains of the future will need to be adaptable. In a world of constant change, the ability to respond quickly and responsibly may be what separates resilient businesses from the rest.
How global supply chains are evolving:
From... | To... |
---|---|
Prioritising efficiency | Balancing efficiency with resilience |
Linear models (make-use-bin) | Circular models (reuse, recycle, repair) |
Global sourcing for cost | Regional or diversified sourcing for risk |
Limited supply chain visibility | Real-time data and full traceability |
Manual forecasting | AI and predictive analytics |
Reporting focused only on direct suppliers | Monitoring the full value chain, including upstream and indirect suppliers |
Reactive disruption response | Proactive risk planning and adaptation |
As supply chains face increasing pressure from geopolitical shifts, labour shortages, climate disruption, and regulatory complexity, resilience has become a defining feature of long-term competitiveness. But what does this look like in practice?
Here are some of the key steps businesses can take to strengthen their supply chains and prepare for the challenges ahead:
Action | What it involves |
---|---|
Diversify suppliers and sourcing regions | Relying on a single country or supplier for critical inputs creates vulnerability. Building relationships with multiple suppliers across different geographies can help spread risk and improve flexibility in times of disruption. |
Map the full supply chain | Many companies have visibility only at the first tier. Mapping upstream and downstream partners – and understanding dependencies at each stage – makes it easier to anticipate bottlenecks, assess exposure, and respond quickly to emerging risks. |
Invest in digital tools and data | Real-time tracking, predictive analytics, and scenario modelling can help identify issues early, optimise inventory, and improve response times. Digital supply chain tools also support better communication and transparency across the value chain. |
Strengthen relationships with key suppliers | Resilience isn’t just about systems – it’s about people. Building trust and collaboration with suppliers can open the door to joint problem-solving, shared risk management, and long-term improvements in performance and sustainability. |
Build in flexibility – not just efficiency | While lean operations have their advantages, they often leave little room to manoeuvre. Resilience means having contingency plans, buffer stock for critical items, and the ability to shift sourcing or logistics quickly when needed. |
Factor in environmental and climate risks | Understanding how climate change could affect key suppliers, transport routes or manufacturing locations is now essential. Physical risk assessments and climate scenario analysis can help businesses plan for extreme weather and long-term shifts in environmental conditions. |
Stay ahead of regulation | With new due diligence and reporting rules coming into force across multiple regions, businesses should review compliance processes, set up systems to capture the right data, and work closely with procurement and legal teams to stay aligned. |
That’s where a structured, data-led approach to decarbonisation becomes essential, and where carbon management solutions can play a leading role.
At Greenly, we help businesses understand and reduce the emissions hidden within their supply chains. Our suite of carbon management solutions is designed to give companies the visibility, data, and strategies they need to take meaningful action.
In a world where supply chains are increasingly shaped by climate risk, Greenly gives you the tools to build resilience and reduce emissions with confidence. Get in touch with Greenly today to find out more.